Latest
News
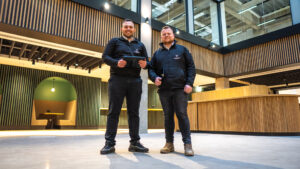
Willmott Dixon Interiors delivers 139,000 sq ft net zero office refurbishment in Birmingham
Read More »
29th May 2025
No Comments
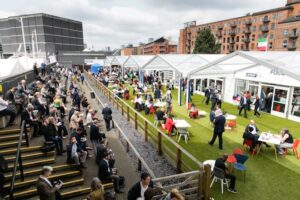
Willmott Dixon Interiors to highlight role of public-private partnerships at UKREiiF 2025
Read More »
7th May 2025
No Comments
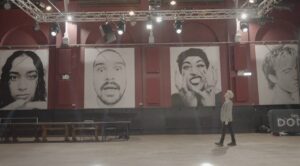
Amazon Prime’s ‘Unsigned’: how we volunteered to transform a venue for future music stars
Read More »
4th February 2025
No Comments